High-performance plastic extrusion solutions for manufacturers
A Comprehensive Overview to the Process and Benefits of Plastic Extrusion
In the vast world of production, plastic extrusion becomes a extremely effective and important process. Altering raw plastic into continual profiles, it satisfies a myriad of markets with its remarkable convenience. This guide intends to elucidate the complex steps associated with this method, the kinds of plastic appropriate for extrusion, and the game-changing benefits it offers the industry. The occurring conversation promises to unfold the real-world influences of this transformative procedure.
Recognizing the Basics of Plastic Extrusion
While it may appear complex at initial look, the procedure of plastic extrusion is basically straightforward. The procedure starts with the feeding of plastic product, in the kind of powders, granules, or pellets, right into a heated barrel. The shaped plastic is then cooled, strengthened, and cut right into preferred sizes, completing the procedure.
The Technical Refine of Plastic Extrusion Explained
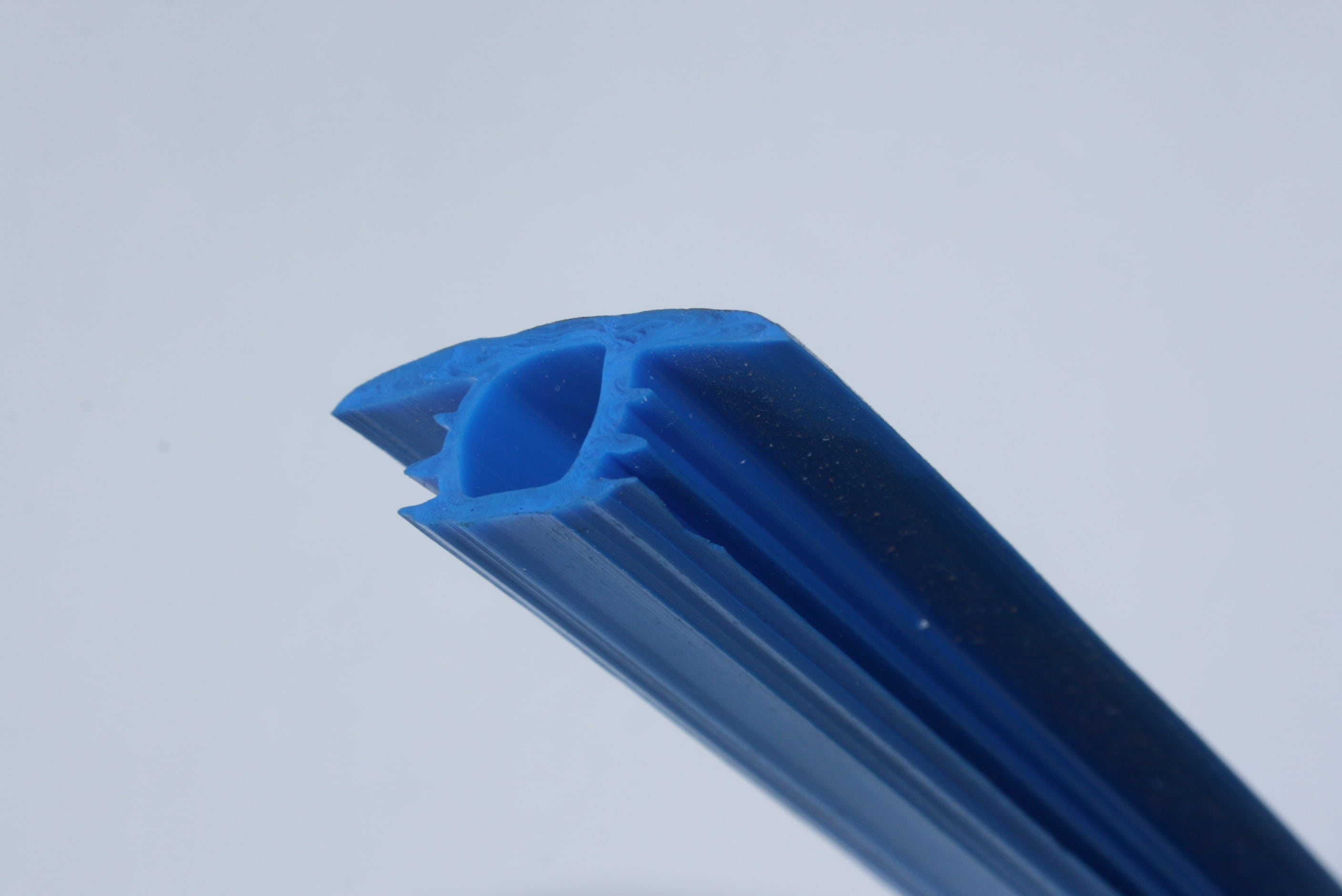
Types of Plastic Suitable for Extrusion
The selection of the right kind of plastic is an essential element of the extrusion procedure. Different plastics provide unique residential properties, making them much more suited to particular applications. Comprehending these plastic kinds can substantially enhance the extrusion procedure.
Comparing Plastic Extrusion to Various Other Plastic Forming Techniques
Comprehending the kinds of plastic ideal for extrusion paves the way for a wider discussion on exactly how plastic extrusion stacks up against various other plastic creating approaches. Plastic extrusion is exceptional when it comes to producing constant profiles, such as seals, gaskets, and pipes. It additionally permits for a regular cross-section along the size of the product.
Key Advantages of Plastic Extrusion in Manufacturing
In the world of production, plastic extrusion supplies lots of substantial advantages. One notable benefit is the cost-effectiveness of the process, that makes it an economically attractive manufacturing method. Additionally, this strategy supplies superior item flexibility and enhanced production rate, thereby increasing total production effectiveness.
Cost-efficient Production Approach
Plastic extrusion jumps to the leading edge as a cost-efficient manufacturing method in production. This process attracts attention for its ability to generate high quantities of product quickly and efficiently, providing suppliers with considerable savings. The key cost advantage is the capacity to utilize less costly raw products. Extrusion makes use of thermoplastic products, which are much less costly contrasted to porcelains or metals. Additionally, the extrusion process itself is relatively basic, decreasing labor prices. Additionally, plastic extrusion needs much less energy than standard production methods, adding to reduced operational prices. The that site process additionally decreases waste, as any type of defective or excess materials can be reused and recycled, offering another layer of cost-effectiveness. In general, the economic advantages make plastic extrusion a highly attractive choice in the manufacturing market.
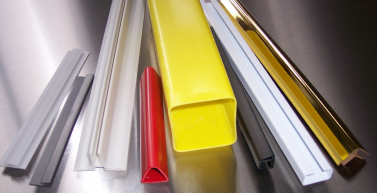
Superior Item Flexibility
Past the cost-effectiveness of plastic extrusion, one more significant benefit in manufacturing lies in its remarkable item versatility. This makes plastic extrusion an ideal option for sectors that need customized plastic elements, such as automotive, building, and packaging. In significance, plastic extrusion's product adaptability cultivates advancement while improving functional effectiveness.
Enhanced Manufacturing Speed
A significant benefit of plastic extrusion lies in its boosted manufacturing speed. Couple of various other manufacturing processes can match the speed of plastic extrusion. see this Additionally, the capability to preserve regular high-speed manufacturing without sacrificing product top quality establishes plastic extrusion apart from other methods.
Real-world Applications and Influences of Plastic Extrusion
In the realm of production, the method of plastic extrusion holds extensive value. The economic advantage of plastic extrusion, mostly its cost-efficient and high-volume output, has transformed manufacturing. The market is persistently striving for developments in recyclable and eco-friendly materials, indicating a future where the benefits of plastic extrusion can be kept without jeopardizing environmental sustainability.
Final thought
In conclusion, plastic extrusion is a very efficient and efficient method of changing raw products into diverse items. It supplies many benefits over other plastic forming approaches, consisting of cost-effectiveness, high outcome, very little waste, and design adaptability. Its influence is exceptionally felt in various industries such as construction, automobile, and consumer items, making it a pivotal procedure in today's manufacturing landscape.
Delving much deeper into the technical you can try this out procedure of plastic extrusion, it starts with the selection of the suitable plastic product. When cooled, the plastic is reduced into the required sizes or wound onto reels if the item is a plastic film or sheet - plastic extrusion. Comparing Plastic Extrusion to Various Other Plastic Forming Approaches
Understanding the types of plastic suitable for extrusion leads the method for a broader conversation on how plastic extrusion piles up against various other plastic forming approaches. Few various other manufacturing procedures can match the rate of plastic extrusion.